コラム
工場力強化の達人に聞く「今取り組むべき製造業の課題」とは?
国際的な競争力の低下や、深刻化する人材不足などによって、日本の製造業はかつての輝きを失っています。それに拍車をかけているのが、長きにわたって製造現場を支えてきたベテランの貴重な技術が、継承されずに失われつつあること。
長年にわたり多くの製造業企業の人材育成、経営管理、品質改善を支援してきたジェムコ日本経営の古谷賢一氏は、「将来的に競争力を保てなくなる企業が増加している」と警鐘を鳴らします。
日本の製造業が抱える教育や技術継承の課題と、その解決法とは何か。古谷氏にズバリ解説していただきました。
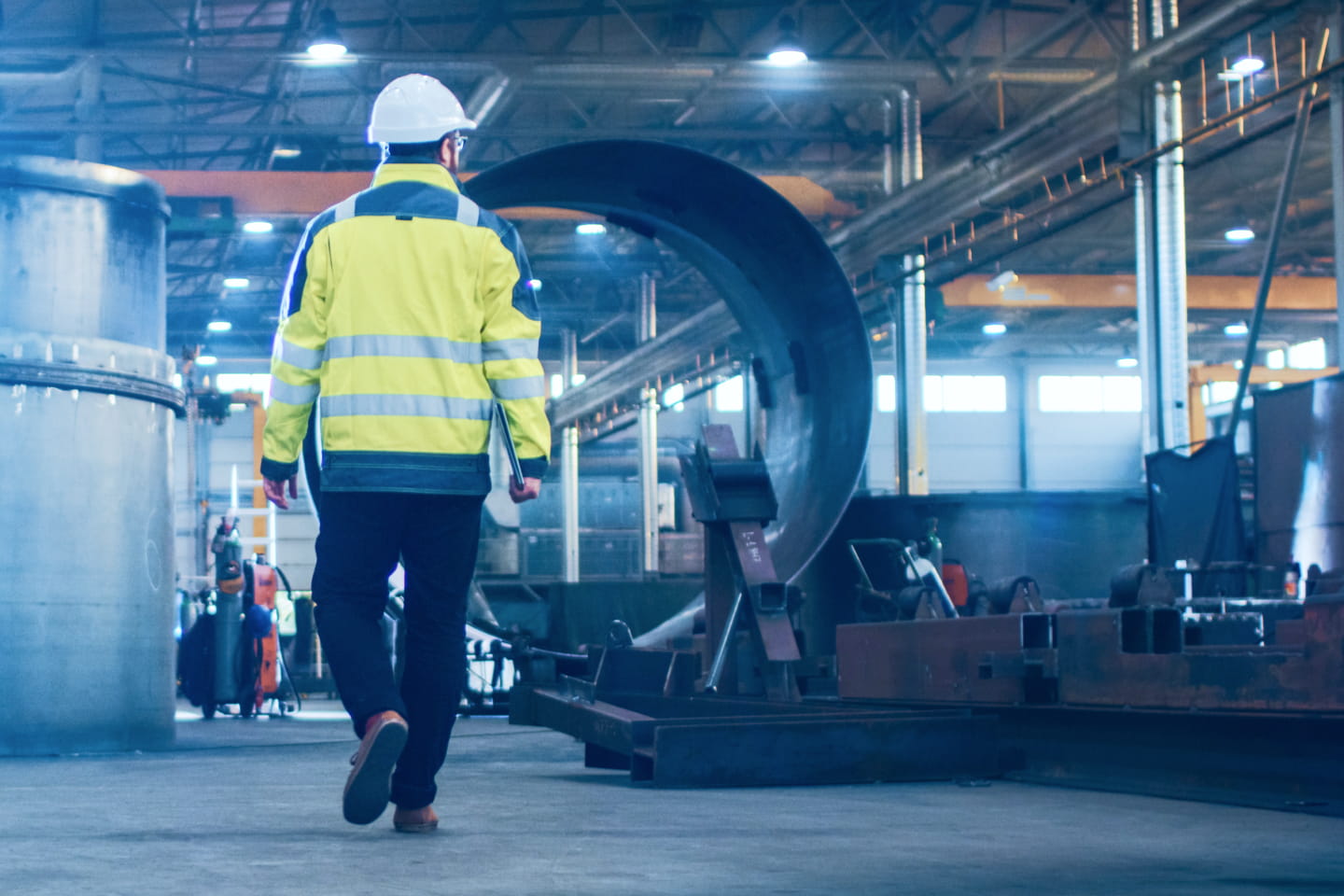
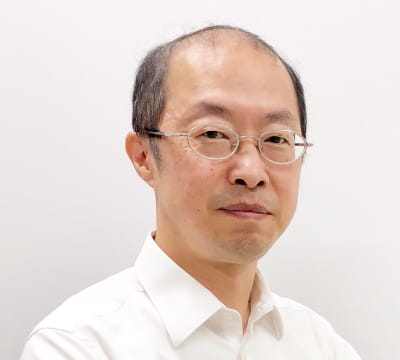
株式会社ジェムコ日本経営
本部長コンサルタント
- 古谷 賢一
- MBA(経営学修士)
大手鉄鋼メーカーの多角化事業部門にて、主に電子回路モジュールおよびコンピュータなど情報機器の開発製造事業に従事。事業子会社の品質保証責任者、生産技術部門長および海外生産子会社(フィリピン、中国)の品質管理責任者を歴任。生産子会社・協力工場や、部材ベンダー・取引先へのものづくり指導、生産技術指導、品質指導を、国内外問わず多く手がけている。
その後、ジェムコ日本経営に入社。経営管理、人材育成から、品質改善支援、ものづくり革新支援など幅広い分野に従事し、“地に足がついた活動”をモットーに、現場に密着し、きめ細かい実践指導は顧客から高い評価を得ている。タイ、マレーシア、フィリピン、ベトナムおよびハンガリーなど、海外での支援実績も多数あり。
将来も今と同じクオリティで生産できるのか? 日本の製造現場の課題
はじめに古谷さんのご経歴について教えてください。
1991年に大手鉄鋼メーカーへ入社、多角化事業部門でパソコンや携帯電話などの開発・製造に携わり、本社より分社した事業会社では品質保証責任者、生産技術部門長、海外生産子会社の品質管理責任者などを務めました。その後ジェムコ日本経営に転職し、コンサルタントとして製造業の企業と数多く関わっています。「現場で実践しやすい指導」を日々心がけています。
日本の製造業に長く関わっている古谷さん。製造業が今まさに直面している課題は何だとお考えですか?
最も大きな課題は、従業員への教育や技術の継承への対応が不十分であることだと考えています。
団塊世代の定年退職、そしてバブル崩壊以降の度重なるリストラによって、製造現場からベテランの方々がごっそりと抜けてしまいました。そのため、労働人口の構成バランスが崩れ、ベテランの持っていた知識やスキル、ノウハウ、暗黙知(※1)などが、新しい世代に伝達されない状況が起こっています。
その結果、新しい技術や製品を生み出しても、量産段階に入るたびに外国企業に市場を取られるなどの問題を引き起こし、日本の製造業が強みを発揮できない原因の一つになっています。
最低限の作業手順は受け継がれているので、今日明日の生産に支障が出ることはありません。「うちはとりあえずうまくいっているから大丈夫」と考えている経営者の方もいるでしょう。
しかし、5年後、10年後を考えたとき、果たして今と同じように生産が続けられるのか? 大きなトラブルが起きたときに適切に対応できるのか? そして何より将来も十分な競争力を保てるのか? こうした問題に直結し、ボディブローのようにだんだんと効いてくるのが現場における教育や技術継承の問題です。 1暗黙知:個人の経験や勘に基づく「コツ」や「ノウハウ」など、言語化されていない知識
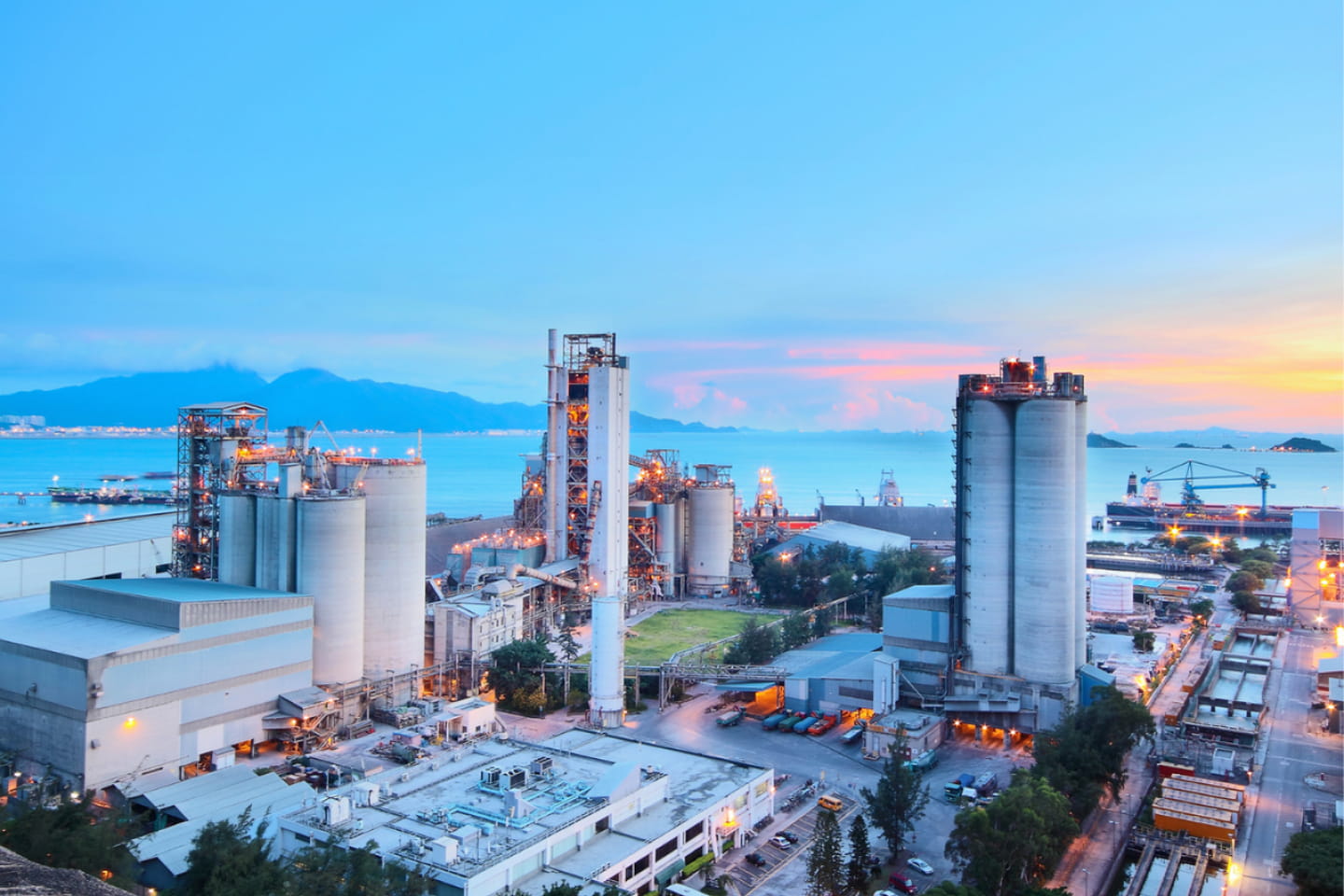
「見て盗め」が通用しなくなった今、「技術継承」の新しい方法が必要に
教育や技術継承は、これまでどうやって行われていたのでしょうか?
日本のものづくりの伝統として、徒弟制(とていせい)にも似た教育法で技術が受け継がれてきた傾向があります。「俺の背中を見て覚えろ」「技は見て盗め」という職人的な教育法です。
たとえば料理店ですと、料理長が全体を采配し、その下位レベルの人が煮炊きや盛り付けを担当し、さらに下位の人がひたすら食材の下ごしらえに従事するケースが多いです。技術や知識レベルの階層構造によって、順を追って技術の習得を行えるよう工夫されています。
しかし、徒弟制のような教育法は、大前提として長期雇用人材を想定しているため、人材が流動化しやすくなった昨今の実情に合わない場面も増えています。ところがベテランの方々の多くは、自らが徒弟制にも似た教育法で育ってきているために、それ以外の教育の仕方が分からないのです。
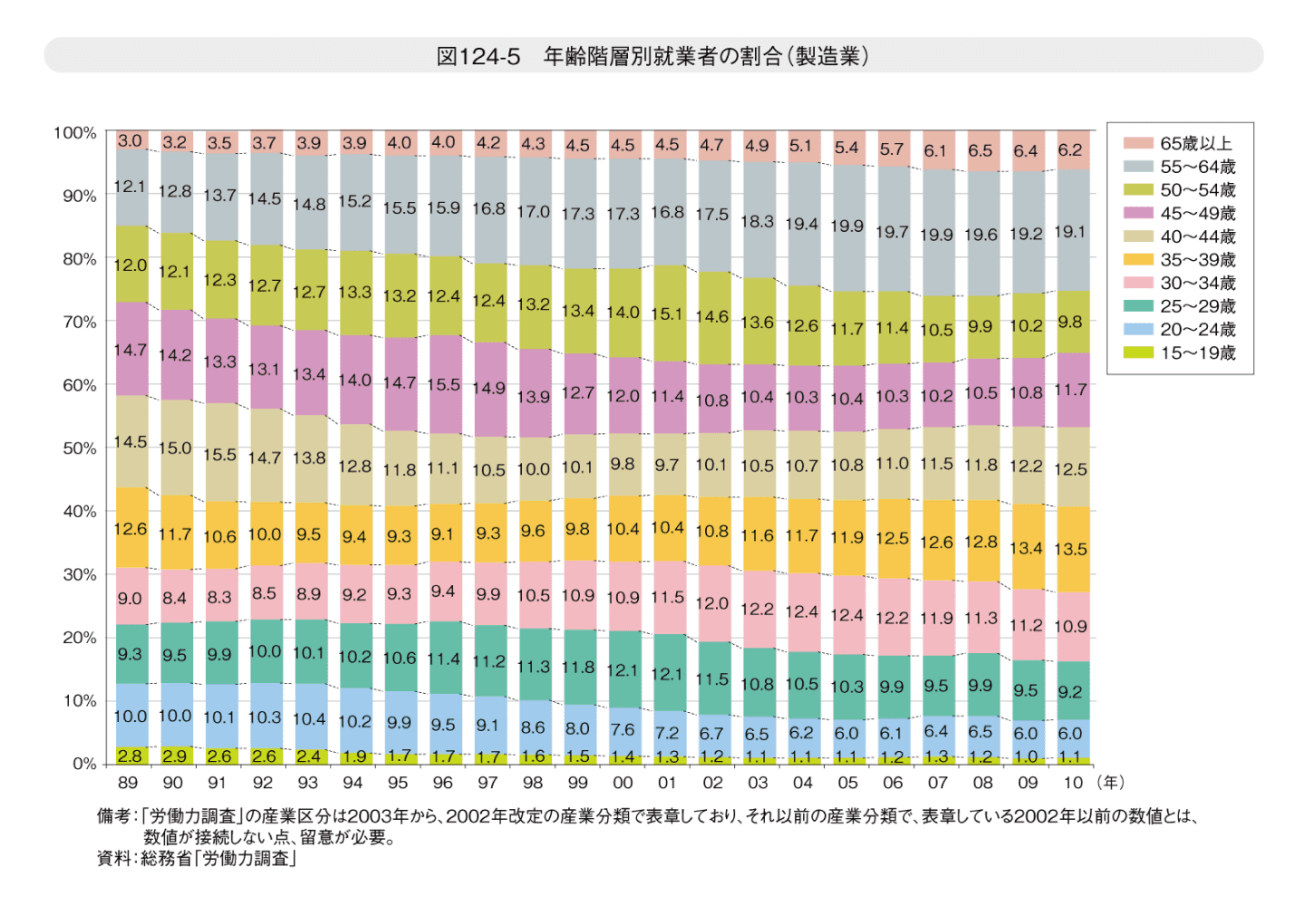
出典:経済産業省「ものづくり労働者の雇用・労働の現状」
40~54歳までの層の割合が減り、55歳以上の増加が顕著に。
90年代以前はバランスの取れていた構成比が、段々といびつな形となっている。
日本の強みである「精緻で複雑な製品製造」には、技術やノウハウの継承が不可欠
作業マニュアルなどがあれば新人でも作業できるかもしれませんが、ベテランに作成してもらうのは難しいのでしょうか。
難しいと思います。暇な工場はつぶれてしまうので、今稼働している工場は基本的にすべて忙しいです。限られた人員で日々の生産を行わなければならず、知識やスキルのあるベテランほど作業に追われています。
直近の生産に支障がでないよう最低限の教育は行いますが、3年後、5年後に必要になるような技術継承や教育を行う余裕はありません。「業務手順書」などマニュアルの作成や、作業の標準化も難しいでしょう。しかし、ベテランはいついなくなるかわからないですよね。
何人もの経営者や工場管理者が「自分たちの時代はうまくできていたのに、今の連中はできない」と言っています。しかしさまざまな知識やスキルを持った人材がすでに抜け落ち始めています。経営者や管理者はそうした現場の状況の変化を理解し、取り返しのつかない状況に陥る前に適切な手を打つべきなのです。
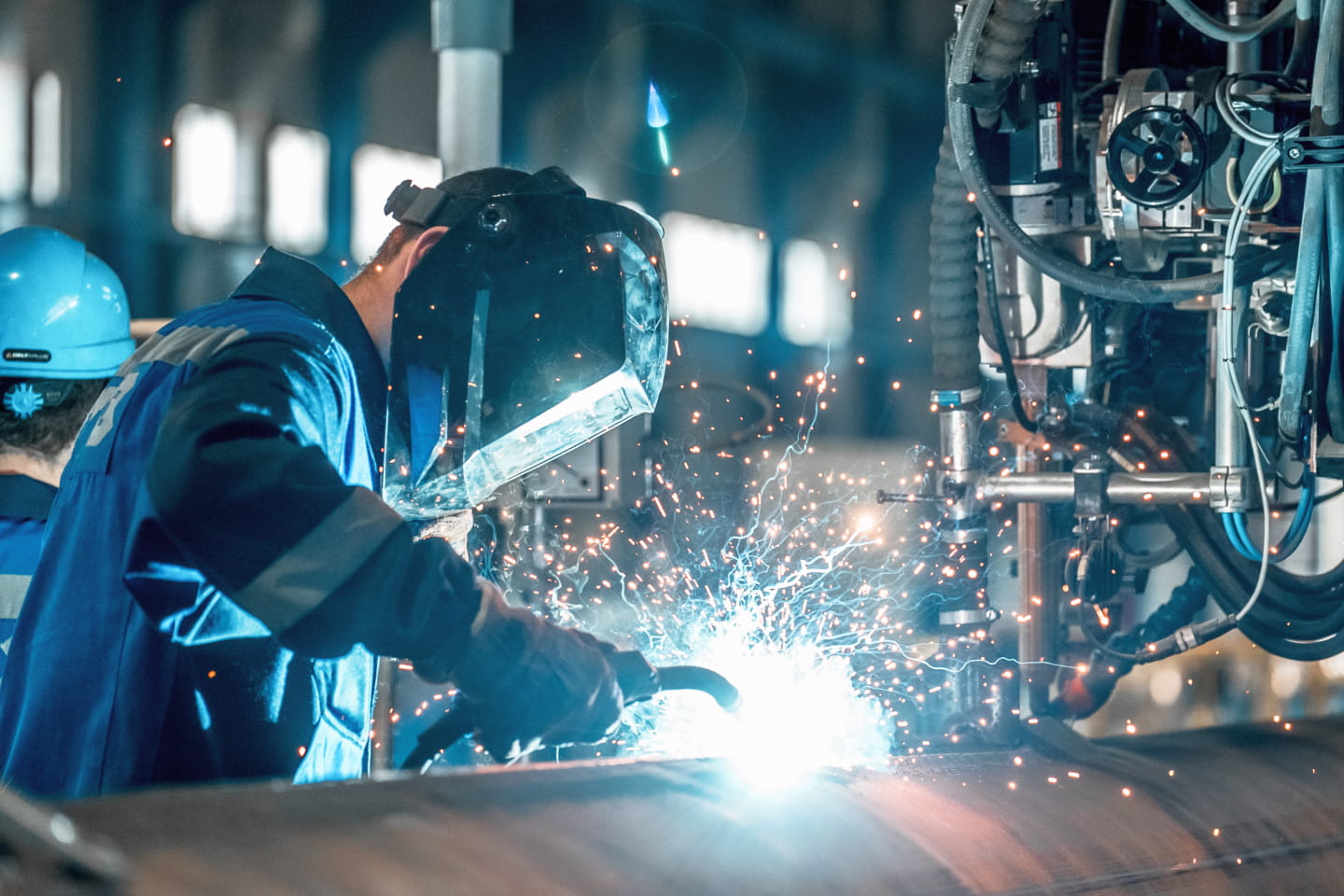
技術継承がうまくいかないと、どんな弊害が生じるのですか?
さまざまな知識やスキルが失われてしまうので、トラブルが起きたときにうまく解決できず、問題が拡大するリスクが高まります。また、生産性の向上など改善活動を行おうとしても、知識不足のため取り組めないという状況が生じます。
欧米のものづくりは「組み合わせ型」、日本のものづくりは「擦り合わせ型」と言われています。欧米の組み合わせ型は、設計、開発、製造など専門の仕事領域と手順を決め、それぞれの専門家が出した成果を組み合わせるスタイル。対して日本の擦り合わせ型は、設計や製造などの担当は決まっているものの、各分野の担当者が担当外の事項についても議論し、知識やスキルを交換することで成果を出すスタイルです。
非常に精密で複雑な製品を生み出すことができる擦り合わせ型こそが、日本のものづくりの大きな強みだと私は考えています。しかし擦り合わせ型を有効に作用させるには、幅広い知識やノウハウ、暗黙知の継承が不可欠です。こうした継承がうまく行えないことには、日本のものづくりの強みを発揮できません。
現場教育を成功させるための2つのポイント
教育や技術継承を上手に行う方法を教えてください
二つのポイントがあります。一つ目は、ほとんど知識がない未経験者や外国人の方でも問題なく作業が行えるよう、業務を標準化すること。書類でも動画でもいいのですが、それを見れば誰でも仕事ができるような作業標準書、業務手順書などのマニュアルを整備する必要があります。教育上手な人材が在籍しているとは限らないので、特定の人に頼らない教育の仕組みを整備すべきです。
もう一つは、ベテランしか持っていない知識や経験、スキル、言葉では説明し難い暗黙知をできるだけ形式知(※2)に変える努力を行うこと。それを組織で共有し、活用できるような取り組みをしてほしいです。
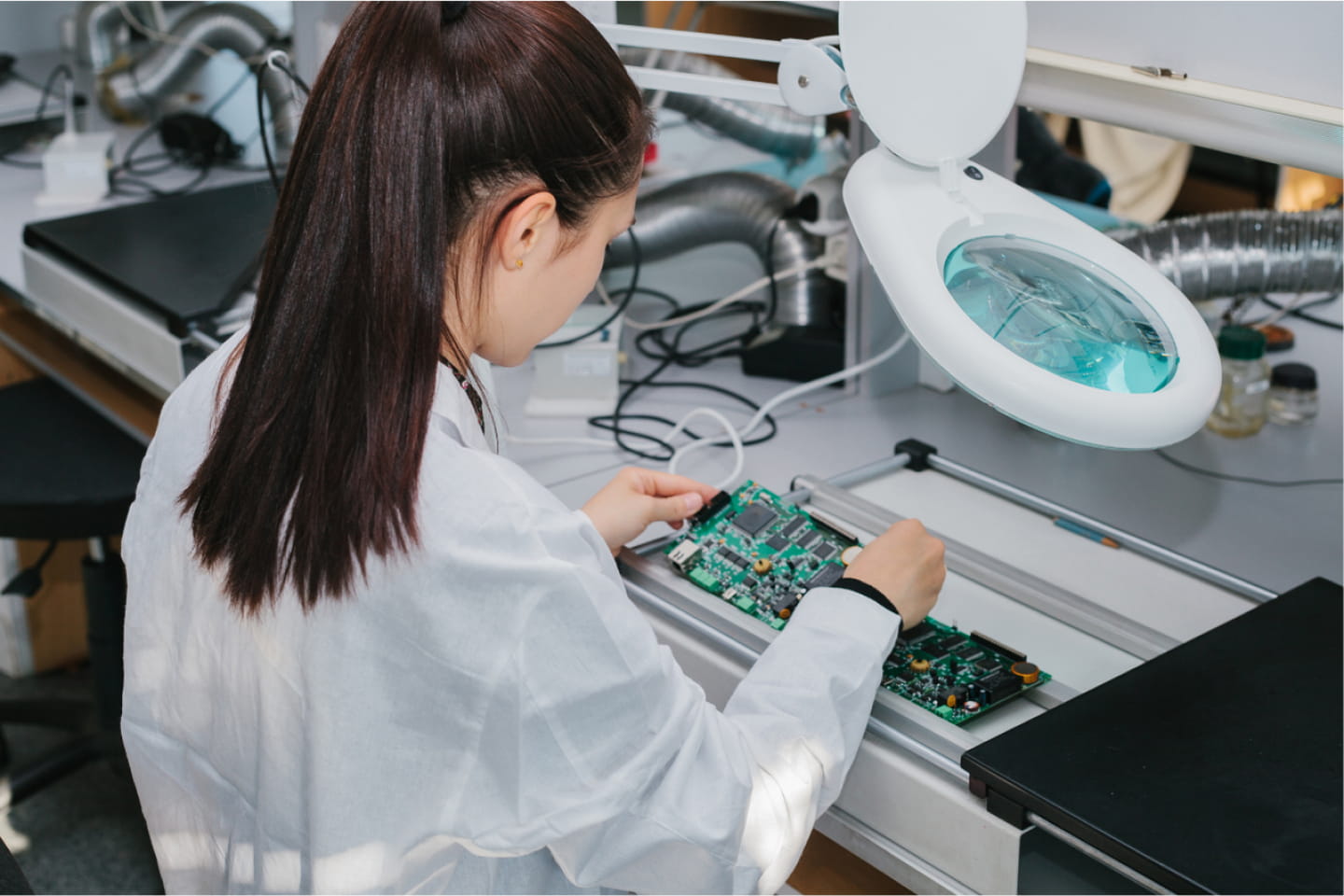
ベテランは忙しく、マニュアルを作る余裕がないと先ほど伺ったので、ベテラン以外の誰かが率先して取り組む必要がありますね。有効な作業標準書、業務手順書を作る上で重要な点は何でしょうか?
仕事のポイントやコツを的確に説明することです。工場の業務手順書には、知識や経験のない人が読んでも理解できないような内容のものが散見されます。
たとえば「部品Aと部品Bをはめ合わせなさい」という単純な指示でも、綺麗に仕上げるにはいくつかのコツが必要な場合があります。しかし、そういったコツは言語化しづらく、結局先輩や上司がやり方を口頭で教えるケースが多いです。それでは生産効率は上がらず、暗黙知も属人化もなくなりません。
だからこそ、誰にでも分かるようなマニュアルを作る必要があるのです。まずは重要工程の一つを選び、時間をかけて分かりやすいものを作ってみてください。それを活用して実際に成果が出れば、もっと作ろうという意欲が湧いてきます。
分かりやすいマニュアルを作るには、テキストだけでなく動画を使うのも有効でしょう。またITツールなどを活用し、誰でもマニュアルにアクセスしやすい環境を構築するのも大切です。 2形式知:言語化され、客観的・論理的に説明できる知識
簡単な動画作成ツールを活用し、ベテランの技を後輩へ引き継ぐ
動画を使ったマニュアルにはどんなメリットがありますか?
文章や写真だけの資料よりも動画マニュアルのほうが、作業のやり方を明確に分かりやすく伝えることができます。また、テロップやナレーションなどの言語を差し替えるだけで、外国人労働者や海外に製造拠点を開設する際の教育にも活用できるのもメリットです。
どこをどのように撮影し、矢印やテロップなどを用いて分かりやすい動画を作るためには、それなりの技術やノウハウが必要になります。ただ、中には動画制作の知識がなくても、直感的に操作できる簡単なサービスもあります。
先ほどのお話に出てきた、ITツールを使った教育の利点も教えてください。
対面による教育は、教える側・教わる側とも工数がかかってくるため、その分生産能力が低下します。しかしITを活用したオンライン教育なら、そうしたロスを減らし、効率的な教育を実現可能です。もちろん、教える内容が重要なのは言うまでもありません。
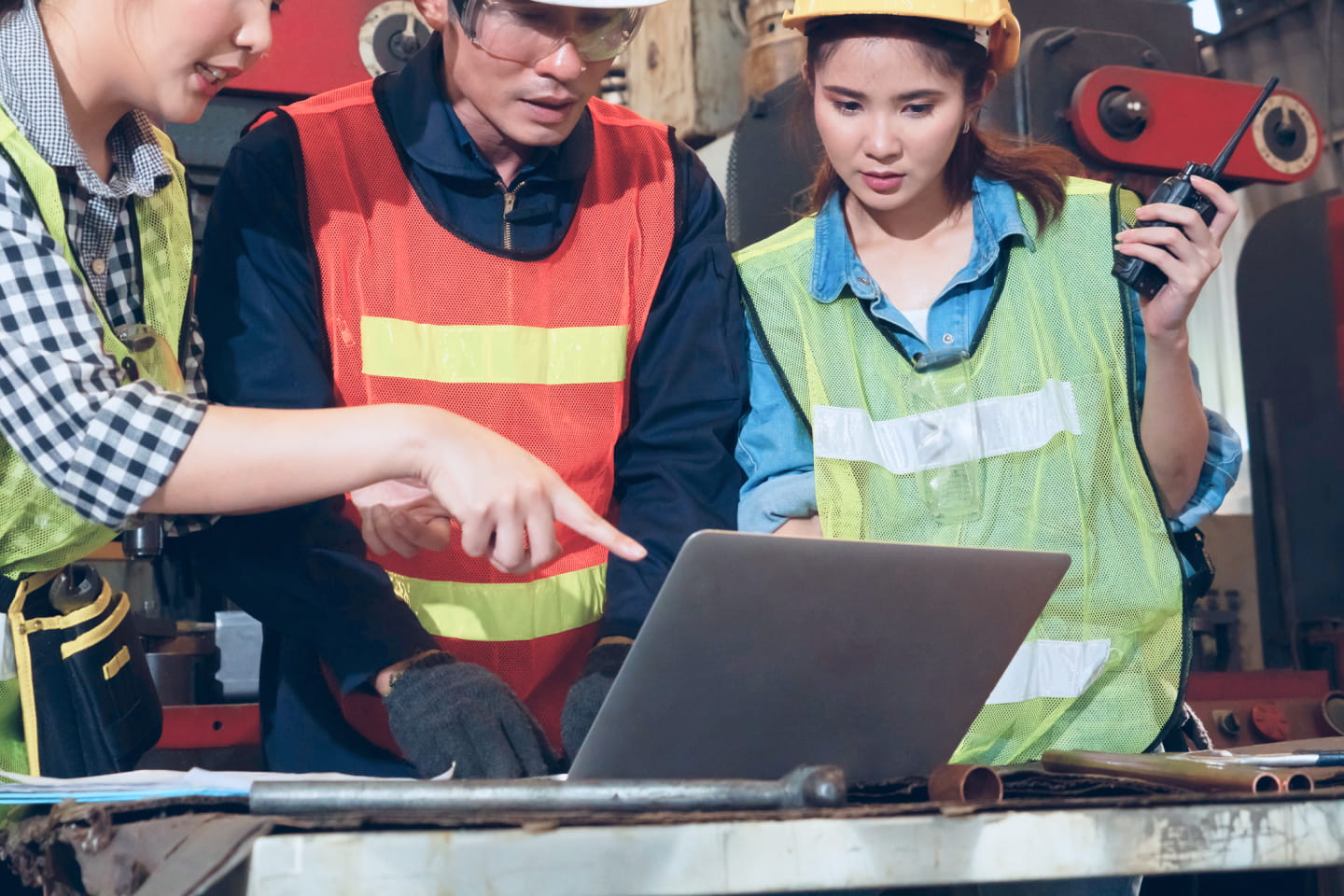
今後、人材不足はさらに深刻化していくと予想されます。どのように対応すればいいのでしょうか?
生産性や品質、競争力の長期的な向上が期待できます。また新人や外国人労働者、さらには海外に設置した生産拠点での教育を効果的に行え、さまざまな問題への対処や改善への取り組みも円滑に実行できるでしょう。
ベテランの技術を継承し、日本のものづくりの強みである擦り合わせ型の特徴を活かすことで、新たな価値を生み出すことが可能になります。
競争力を持ち続けるには、技術継承への投資が不可欠
工場力を高めるために、工場管理者や管理職が心がけるべきことは何ですか?
製造現場で実務を行う視点だけでなく、長期的に取り組むべきことや現場のあるべき姿を指摘できるような「経営者の視点」を併せ持つことが重要です。
たとえば、私が数年来コンサルしている会社では、毎年工場長や所属長の推薦で課長クラスの人材10人を選抜し、経営者視点を養う育成プログラムを行っています。彼らは現場目線と経営目線での議論が可能です。私の知る限り、そうした人材を擁する企業は、業界で優位を保っています。
その際、経営陣はどのような役割を果たすべきなのでしょうか?
工場の管理者や中間管理職が教育や技術継承の必要性を感じていても、いざ改善しようとすると自分たちの業務量が増えてしまうので、なかなか言い出せないケースが数多くあります。
そのため経営層が舵を取って、必要性を強く発信して管理職に行動を促したり、インセンティブを活用したりすることで、改善を推進する仕組み作りを行うことが必要です。
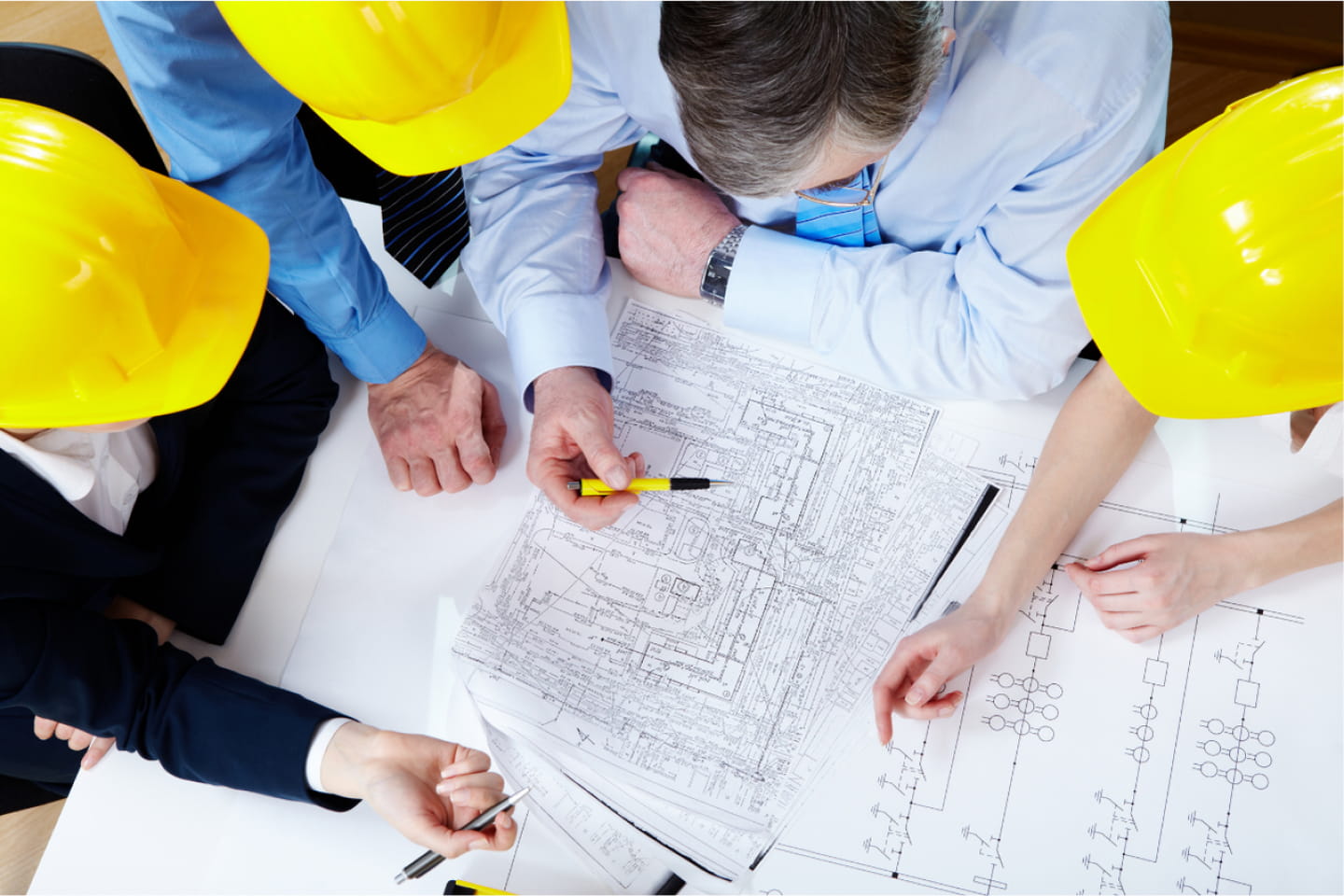
少子高齢化や生産年齢人口の減少により、人材不足はさらに深刻化すると予想されます。どのように対応すればいいのでしょうか?
繰り返しになりますが、未経験者や外国人労働者など、誰でも作業できるような業務の標準化を進めるとともに、分かりやすいマニュアルを整備することが大切です。
そして必要に応じて、ITツールやシステムの導入を検討します。「新しいツールを導入したら状況が改善する」と考える担当者もいますが、目的は導入することではなく、それを活用して成果を出すこと。ツールを「どう使うか」で企業間の強さに差が出ます。
誰にでも分かりやすいマニュアルを作るために動画やクラウドを活用するなど、実現したい理想を想像し、そこに近づけるツールを使う。そんな組織はさらに強くなっていきますよね。
最後に、製造業に関わる皆さんへアドバイスをお願いします。
ここでお話ししたことは「そんなこと知ってるよ」と感じる方が多いかもしれません。
しかし大切なのは当たり前のことをどこまで徹底できているか。今も成長している製造業の企業は、当たり前のことを徹底し続けているのです。
今すぐに困っていなければ危機感を持つのは難しいかもしれません。しかし放置すれば、数年後、数十年後には技術や知識が確実に失われます。
私の経験から言えるのは、業績の良好な会社ほど、自社の足りない部分や課題についての議論を活発に行っているということ。現場と経営の両方の視点から課題を見つめ、解決のために行動を始めることが重要です。